Push Rod Bearings - Heim Bearings
There are 11 Heim Rod End Bearings in the Ercoupe Control System. These bearings will be found at the following locations:
Assembly | Assembly
Part No. | Heim No. | Erco
Bearing No. | No. of Bearings
per Airplane |
Pushrod; aileron to bellcrank Pushrod; ail. cont. mast to bellcrank Pushrod; control column to mast Shaft and column assy.; control Shaft and column assy.; control | 415-52034 415.52038 415-52036 415-52117 415.52117 | MD36-14 MD36-14 MD36-14 MD36-14 MD36-14S | 415-52034-2 415-52038-2 415-52036-2 415-52117-18 415-52117-23 | 4 4 1 1 1 |
alternative part Aurora GMM-3M-670 These bearings are supposed to be lubricated every 300 hours. Since the proper lubrication procedure will require a total disassembly of the control system to gain access to every each of the bearings, so you can grease them with a grease gun in an adapter that you would have to fabricate yourself - an instruction on how to make one yourself is found here: How to make a greasing adapter
If you don't lubricate the rod ends in intervals, you'll end up with dried out bearings that will corrode over time like the one pictured below.
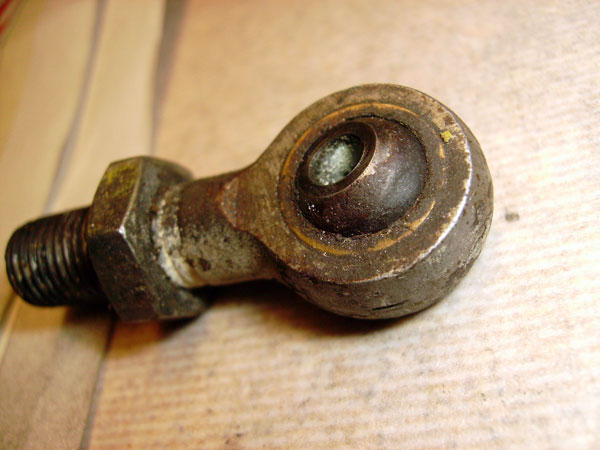
A corroded bearing needs to be replaced. It is cause for slack and play in the control system. If you have many of these bearings, your controls are sloppy and might even start to flutter. It also surely adds to nose wheel shimmy.
If you experience excessive play in the controls, you most likely have to replace some of the bearings. But it is also advisable to replace all hardware fasteners as well. Follow the Ercoupe catalog pages and get the right fastener for the your bearings. For example, clevis bolts are specified for one side of the aileron pushrods. The pins have a greater shearing resistance and the way the control system is designed we will find higher and lower forces acting throughout the system.
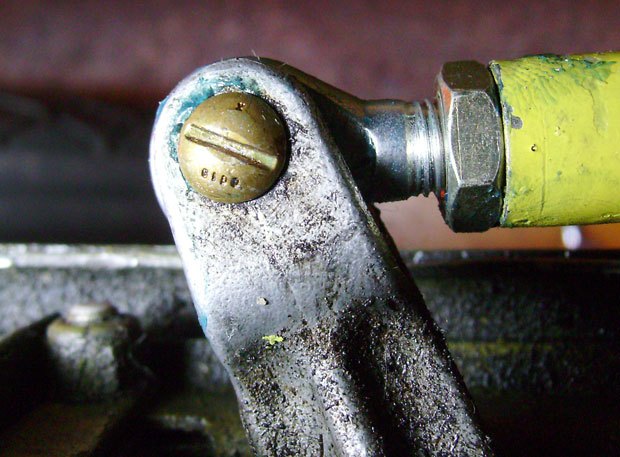
Using new and proper hardware takes out already some of the slack in the controls.
On my Ercoupe there were bolts used with a too short shank. This is a no no, because the threaded part is smaller than the bolt and the bolt will be loose in its guide.
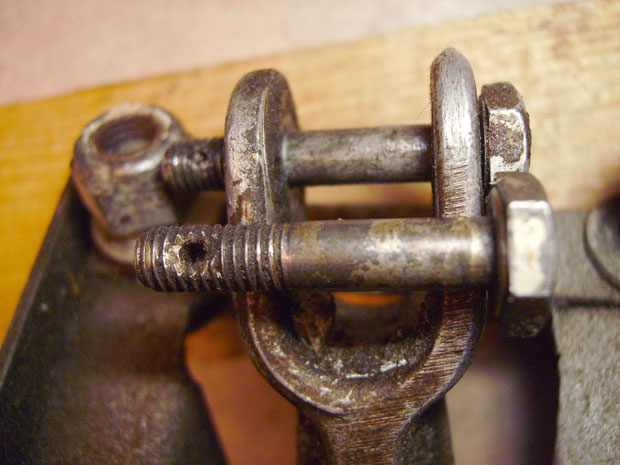
The grip of the bolt in front is too short for the aileron bellcrank. The bolt was sitting with its threaded part in the bellcrank. The threaded part is smaller in diameter than the grip. Now the bolt would "work" in the hole, because no matter how much you tighten the bolt, the hole in the bellcrank is bigger than the bolt. Every pull or push will work the threads of a high strength bolt against the aluminum cast bellcrank. The threads are acting like a file, so the hole is getting elongated and you end up with more and more play. Always use the right size bolts and clevis pins here.